Technical Newsletter vol.6 : 3D-MIM
3D-MIM mass-produces complex designed metal parts with high precision
Machining is a typical method of precision machining. However, processing costs increase in proportion to required accuracy and shape complexity. Moreover, from the viewpoint of material yield and processing time, it is not suitable for large-scale mass production of especially complex designed metal parts. Meanwhile, our 3D- MIM, which we developed independently, is capable of stable mass production of complex designed metal parts having same level of precision as machining. In addition, because of the high degree of design freedom, it is possible to integrate multiple parts, and it is expected to reduce the processing cost, the number of processes, and the number of parts greatly. It is also possible to mass-produce the parts with hollow structures that cannot be demoulded such as undercuts, many micro cavities, those which cannot realise in ordinary mould design. Specifically, as shown in the figure below, we make a resin core (sacrificial mould) and over mould the MIM material to form the final shape of the metal part. Remove the injected part from the mould while remaining the resin core, and then decompose and remove the core and the binder component in the MIM material in the subsequent process.
We will mass produce the design as you wish
In the MIM industry, there are many companies based on metal powder manufacturers or metal processing manufacturers. However, we have been developing MIM technology based on our plastic injection moulding manufacturing history, so our injection moulding technology is one of the best among MIM industry. Let us introduce an example. It is impossible to fabricate parts with a branched flow path with many free-form surfaces inside as shown in the left figure, by machining. Also it can be said that not all MIM manufactures realise this design because it is required high moulding technology. The shape can be obtained by using the latest additive manufacturing or metal 3D printing technology. However, due to the rough surface finish, it cannot be used as a flow path. Our 3D-MIM technology realises mass production of complicated designed metal parts with smooth surface.
COLUMN
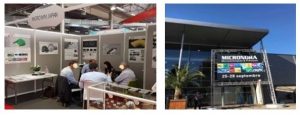
Micronora on 25-28 September 2018
Izumi Nakamura from the German office. For the first time, we exhibited at Micronola, the world’s largest microfabrication technology exhibition held once every two years in Besançon, France on September 25-28. There are many visitors who belong to their technical purchasing and development departments of European companies not only from France, but Switzerland, Germany, Italy, and so on. They were eagerly visiting various booths to see the latest micro technology and discuss to apply their products. 35% of the exhibited companies were foreign companies like us. What I was surprised at was that just after the opening time, 9 am, we heard a sound of opening a champagne at a nearby booth! When a big business negotiation is decided, it seems common to send champagne to the customer in France. Many existing and new customers also dropped in at our booth. It was a pleasure that most of visitors already knew well about MIM.
*Remark : This newsletter was originally published on November 6, 2018