Gear processing
Gear processing
The process of gear is usually expressed as ‘gear cutting’ because machining or cutting is the only process to achieve gear requirement such as complexity and high precision. It is employed a dedicated special-purpose machine known as an NC gear processor or gear grinder, with a special cutting tool which designed to satisfy the required tooth profile and the specifications. However, our μ-MIM technology has developed a gear mass production by MIM without the post machining.
Gear types
In fact, even the term ‘gear’ itself includes wide-ranging shapes, processing of which requires a dedicated and purpose-built machine. With the initial distinction made between “spur gear” and “bevel gear”, dedicated gear cutting machines used in each case are known as ‘spur tooth’ and ‘bevel gear’ cutting machines. Moreover, the scope also includes helical gears, with spiral fluting, ‘rack and pinion’ devices that convert rotary to linear motion and cylindrical worms, with which rotary motion is converted to vertical motion.
- Bevel gears
Bevel gears feature designs in which the axes of both shafts interest and the tooth-bearing gear faces themselves are conically shaped. Depending on the tooth shape involved.
- Helical gears
Helical gears are cylindrically shaped with helicoid teeth and widely used, since they are durable and quieter than spur-type gears. They generate axial (thrust) force while in use.
- Spur gears
Spur gears are cylindrically shaped, with teeth parallel to the axis and their ease of manufacture makes them the most popular choice of gear for power transmission.
- Rack & pinion gears
In these gears, a circular gear (the pinion) generates rotary motion, which is then translated into linear motion when teeth on a linear gear bar called the gear rack are engaged. Applying rotational force to the pinion causes the rack to move horizontally to the toothed end.
- Worm drives & worm wheels
Reducing the number of teeth on the bevel gear to one or a few, it becomes like screw, which gear is known as a ‘worm’. The worm-like screw thread meshes with a larger gear (worm wheel) with teeth cut at various angles, which are driven when the worm rotates in a set-up known as a worm drive.
- Internal gears
The gears with teeth on the inner surface of a cylinder or cone. When two external gears are meshed, the rotation directions oppose each other but an internal gear features both input and output shafts rotating unidirectionally. The internal gear also features a higher number of meshing teeth than external gears for correspondingly quieter transmission and there is scope for deployment within the AT planetary gear mechanism in epicyclic gears. In recent years, aimed to reduce noise, internal gears with helicoid teeth are becoming increasingly popular.
Materials for gears
The main materials used in gears have typically been SC steel or alloy steel. However, wear resistance, weight reduction and corrosion resistance have become priorities in recent years, the range of materials required from various perspectives.
On the other hands, the numerous materials are difficult to cut, while the additional emerging requirement for complex shapes has seen MIM production (metal powder injection moulding) come to the fore.
Our company has fielded numerous enquiries, including for gears using stainless and titanium alloys.
Gear processing by MIM
With the advent of Industry 4.0, the trend of a new and robot-centric industrial revolution has been embodied worldwide.
The scope of robot technology transcends manufacturing production sites alone to encompass a far wider range of fields, including medical and nursing care, agriculture, construction and infrastructure work. Considerable efforts have also been made in many countries, given the potential to solve social issues such as eliminating labour shortages, easing the need for heavy labour and boosting productivity. Increasing functional diversification, in drive systems above all, has sparked an equivalent surge in the range of development efforts, including reducing costs, boosting strength, accommodating complex shapes, increasing precision and miniaturisation.
(In this case, μ-MIM, which paves the way for innovative gear cutting, should be uppermost in mind!)
In MIM gear production, it is not required to prepare any back up special tools once mould toolings is completed. Also while allowing strength and geometric tolerance to be maximised by integrating parts of any shape such as intermediate gears with differing specifications and phases, stepped gears with differing modules. Moreover, when it comes to combining multiple gears and integrating with other parts where machining alone will not suffice, a free of tooth and tooth root design are feasible. Size constraints dictate that special tools are needed when small-module gears are machined and it is very frequenctly damage to the cutting edge thus, the processing cost will be increased. On the other hand, our μ-MIM approach in relevant areas can elicit numerous benefits. Additionally, unrivalled our advanced measurement and evaluation of gear techniques promote more consistent quality management.
- Small module : Mass production capable of micro gears
- Exceptional productivity of micro gears -
Capitalising on the high-precision mass productivity of µ-MIM realises modules of 0.5 or less can be successfully produced with satisfying tight tolerance requirement. This method even paves the way to mass produce internal and helical gears, in the order of one million units per month which are difficult to realise by machining. It is also well-suited to small-diameter internal gears, in fields where other processing methods would be infeasible.
Multianit gear: When space and budget are limited
- Integrating shafts and gears reduces the parts number -
The set screw, key, pin and spline are usually employed to assemble the gears to the shafts. However, the MIM approach allows integrated manufacturing which leads reducing the numbers of parts and improving the strength with satisfying the tight tolerance requirement. For all drive parts, there is now scope to respond to the ever-increasing demand for miniaturisation by issuing more affordable and space-saving proposals following a design review.
Special Gear: Mass production of innovative designs
- Applied in the latest medical equipment-
MIM’s unrivalled scope for almost free design limitation can also accommodate special gears such as, special designed toothed, non-circular, intermittent and so on. The fact that it is manufactured from a mould also cope with eccentric gears, where ensuring shaft accuracy would otherwise be difficult. Manufacturing the internal gear integrally right up to the bottom also means the casing can be mass produced.
Measurement and evaluation of small modules and special gear
Leveraging the latest X-ray CT techniques and gear analysis software, 3D structural and CAD data can be compared and verified, as well as shapes of parts and accessories, including small-module gears, internal helicoid toothed components and other specially shaped gears which normal probes and image measurement machines cannot assess.
* Pitch error, tooth thickness, tooth type, tooth error, tooth surface error, grade indication (DIN-, AGMA-, JIS-compliant)
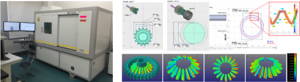
Indicates the accuracy of the tooth profile, expressed as the maximum/minimum difference of the tooth profile from tip to root. Helix form deviation:
Indicates the accuracy of the tooth flanks and expressed as the difference between the maximum and minimum tooth widths in terms of tooth thickness. Pitch error:
Indicates the tooth indexing accuracy, expressed as the pitch error adjacent to the gear and the accumulated pitch error. Tooth gap runout accuracy:
Indicates the positional accuracy (runout accuracy) of the tooth groove, as indicated by the variation in the radial position of the ball pushed into the tooth space.
MIM examination of existing gears
If you have gear products processed by machining, additive manufactured, in trial or in mass production, please do not hesitate to contact us. We can also provide reverse engineering from finished components. There may be scope to further strengthen or improve the accuracy with produced by our µ-MIM technology.