What's New MORE
- 28,Jan,2022
- News
- Webinar archive -“Incus x Micro MIM Japan Lithography-based Metal Manufacturing to complement MIM production” presented by Micro MIM Japan Holdings.
- 6,Jan,2022
- Event
- Micro MIM Japan Holdings Inc. Webinar on 27th January, 2022
- 21,Dec,2021
- Technical Newsletter vol. 33 : Problem solutions in MIM process; debinding and sintering process
What's μ-MIM®
μ-MIM® is a next-generation MIM technology developed by Micro MIM Japan
- High-precision process
- Our μ-MIM® has achieved tolerance to within 10 μm, which is an accuracy equivalent to machining. In comparison, conventional MIM only achieves tolerance to within 50 μm.
-
- The widest material selection range
- We have experienced production of ferrous (standard stainless steel to magnetic, carbon steel), non-ferrous (titanium, copper alloy, tungsten alloy) and precious metals (platinum, gold, silver) alike. Moreover, we also accept new composites or alloys to develop new materials.
-
- Great design freedom
- μ-MIM® makes mass production possible for even complex designs. For example, hole structures with under-cuts, free-form surfaces, thin wall structures under 100 μm, functional surface morphology design and so on.
-
- Processing cost reduction
- When it comes to mass-producing compact and complex design components, μ-MIM® achieves significant processing cost reductions. Savings are also possible with otherwise difficult-to-process material components.
- Quality assurance
- Unlike other SME metal component manufacturers, we have the latest X-ray CT scanners, SEM and optical measurement systems to support our quality control. 100% visual inspection in process is also possible.
-
- Solution support
- Our R&D section will strive to help solve your technical issues. Exceptional value and one-of-a-kind features are made possible by our unique technology.
-
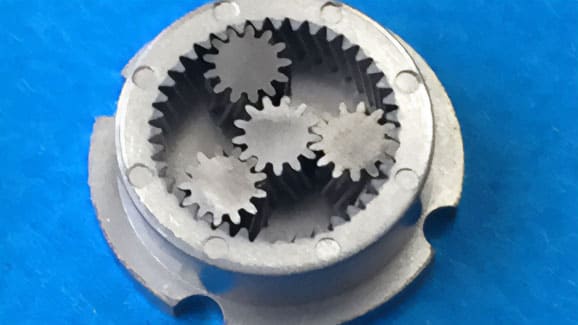
Helical Gear
- Material
- Stainless steel 316L
- Advantage
- Successfully manufacturing micro gears otherwise impossible with CNC machining
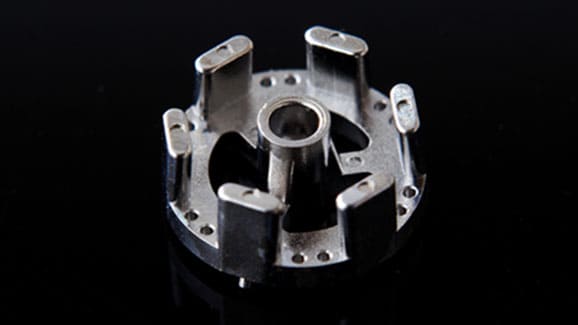
Soft Magnetic Yoke
- Material
- Stainless steel 410L
- Advantage
- Eliminates the magneto–striction that comes when machining soft and complex-shaped magnetic parts
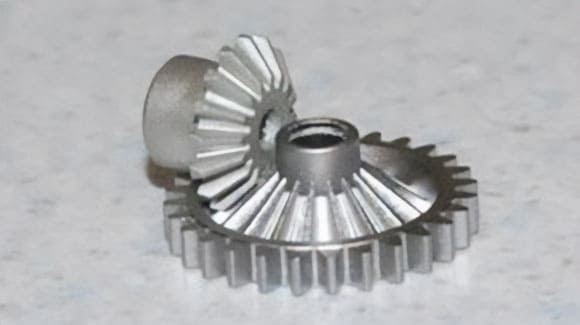
Bevel & Miter Gear
- Material
- Stainless steel 304L
- Advantage
- Cost-cutting: switching from CNC machining to an MIM process.
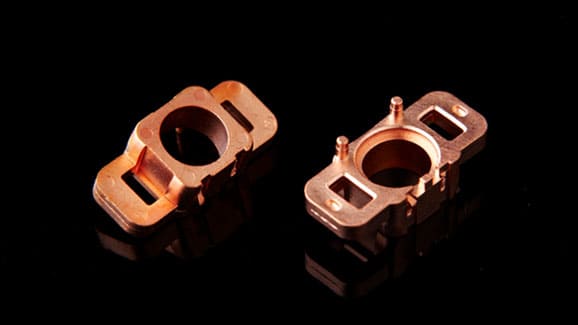
Heat Sink
- Material
- Pure Copper
- Advantage
- Successfully manufacturing compact Cu parts for which CNC machining would be uneconomical
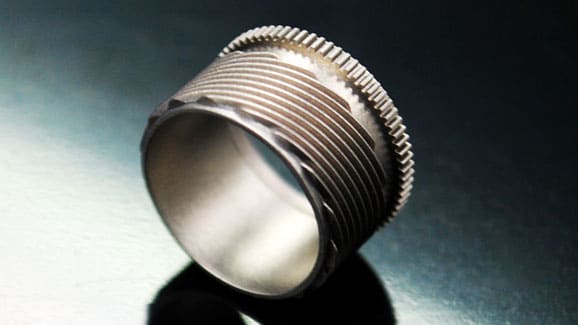
Helical Gear
- Material
- Stainless steel 630
- Advantage
- A helical gear, difficult to mass produce, is realised by μ-MIM
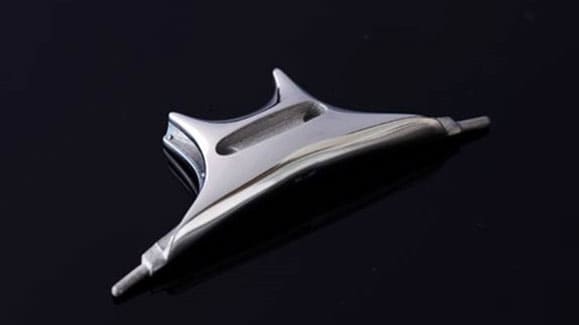
Eyewear parts
- Material
- Pure Titanium
- Advantage
- Its free-form surface is unsuitable for CC-machined serial production.
Company logo
Our company logo uses red, just like the Japanese national flag. Taisei Kogyo Co., Ltd. was established as a plastic injection moulding manufacturer in the 1970s and we have adapted metal injection moulding (MIM) technology based on our plastic moulding experience. MIM technology was originally developed in the United States, since which time Taisei Kogyo has developed new-generation MIM, μ-MIM® technology, in Japan. We respect the invention and are grateful for the existing MIM technology. From now on, however, we would like to transmit our μ-MIM® technology as a Japanese company.
This logo has a shape intertwined with an image letting you grab the future with your own hands. This hand also seeks a new form by repeating trials, with which we will positively explore the potential for new manufacturing enterprise in the market.
Do you have any questions?
Micro MIM Japan Holdings Inc. has a wide reach across the globe.
Please do not hesitate to contact us if you have any questions.
We look forward to hearing from you and will get back to you as soon as possible.